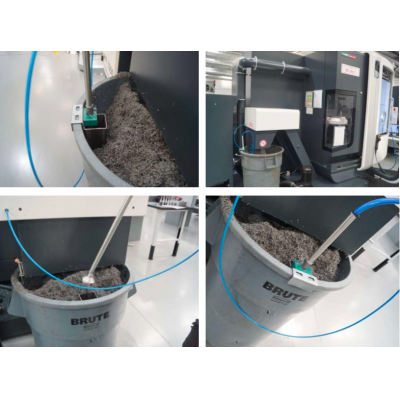
Der bei Progressive Technology eingesetzte Wogaard-Kühlmittelsparer .
Das in Newbury ansässige Unternehmen Progressive Technology, das fortschrittliche CNC-Bearbeitungsdienste für die meisten führenden Branchen der High-Tech-Branche anbietet, hat sich in seinen Methoden und Fähigkeiten erheblich von den Anfängen des Unternehmens verschoben. Geografisch hat es sich jedoch kaum bewegt, da das familiengeführte Unternehmen ursprünglich in Overton außerhalb von Basingstoke, weniger als 30 Minuten entfernt, gegründet wurde. Als der Firmeninhaber 1995 das kleine Vorrichtungs- und Werkzeuggeschäft von seinem Vater übernahm, investierte er in Drahterodier- und CNC-Bearbeitungstechnologie, um die damaligen Kundenbedürfnisse zu erfüllen.
Vor rund sieben Jahren investierte das Unternehmen in die 5-Achsen-CNC-Bearbeitungstechnologie, als ein Formel-1-Zulieferer mit Sitz in Newbury beschloss, seine Werkzeuge aufzuhängen. „Wir haben das Gebäude und einen Teil des Werkzeugmaschinenvermögens erworben“, erinnert sich Verbesserungsingenieur Ashley Mizen. „Obwohl wir das Geschäft nicht übernommen haben. Die Motorsport-Kunden haben auf uns gewartet, um die verbleibende Lücke zu füllen. Wir hatten die Ausrüstung und die Kapazität, also haben wir unser Ingenieurwissen auf die verschiedenen Projekte angewendet und es ist von dort gewachsen.
„Wir hatten damals den 5-Achs-Standort in Newbury und die Dreh- und Vertikalfräsmaschinen in Overton. Wir sind von Kraft zu Kraft gegangen und haben das gesamte Fräsen an den ursprünglichen Standort in Newbury verlegt. Mit der Anschaffung weiterer Maschinen kam es zu einem Zeitpunkt, an dem wir platzen konnten. Wir begannen, uns in Newbury nach anderen Standorten umzusehen und kauften dann vor etwa drei Jahren unsere derzeitige Anlage. “
Nach einem umfangreichen Sanierungsprogramm war das 5.000 m2 große Aggregat bezugsfertig, die Möglichkeit, zwischen den Stoßzeiten der Motorsportsaison zu wechseln, bestand jedoch nur aus zwei Wochen. „Wir haben die von uns gelagerten Werkzeugmaschinen umgestellt und einige andere ersetzt. Unser alter Mikron wurde mit einem neuen Mikron HPM600U aktualisiert. Zwei neue DMG 40 eVos sowie zwei neue DMG 60 eVos wurden ebenfalls in die Anlagenliste aufgenommen “, sagt Ashley Mizen.
Diese Investitionsphilosophie hat sich mit dem Wachstum des Unternehmens fortgesetzt. Neben zwei neuen 5-Achs-Hedelius-Bearbeitungszentren und einer DMG DMU 50 wurden drei 5-Achs-Musterbearbeitungszentren von CMS hinzugefügt. Er fährt fort: „Wir sind ein schnell reagierendes Unternehmen. Wir haben ein Auftragsbuch, das tendenziell stark schwankt. In Zusammenarbeit mit allen großen F1-Teams investieren wir ständig in neue Technologien. Wir legen großen Wert auf die Spezifikation unserer Maschinen. Viele zusätzliche Funktionen sorgen dafür, dass sie so effizient und vielseitig wie möglich sind. “
Heute sind die 60 hochqualifizierten Mitarbeiter 7 Tage die Woche rund um die Uhr beschäftigt. Die zu schneidenden Materialien umfassen eine breite Palette an technischen Kunststoffen, rostfreien Stählen, wärmebehandelten Werkzeugstählen, Aluminium der Serie 7, Titan und hitzebeständigen Legierungen wie Inconel sowie Silizium-Einschlussmetallmatrix-Verbundwerkstoffen mit PKD-Werkzeugen. Alle Mitarbeiter haben die Befugnis und das Vertrauen zu liefern, wie Ashley Mizen sagt: "Es geht darum, sicherzustellen, dass die richtigen Jobs an den richtigen Ingenieur gehen."
Die Losgrößen variieren, Motorsportkunden können 12 Teile bestellen. sechs von jeder Hand, wohingegen medizinische Präzisionskomponenten normalerweise 500 aus sind. „Eines der größten Probleme für uns ist, dass wir mit viel Hochdruck durch das Spindelkühlmittel maschinell arbeiten. Daher neigen die Maschinen zum Fluten, es sei denn, wir halten die Späneförderer ständig an. Dadurch werden die Späne jedoch bald mit Kühlmittel gefüllt. "
„Als sich die Regeln für Altmetall vor kurzem geändert haben, haben wir uns für einen Dienstleister aus einer Hand entschieden, der jedoch nicht wollte, dass unser Altmetall nass wird. Wir hatten ein System, bei dem die Spänefächer auf ein Gerät geladen und dann zum Entleeren gekippt wurden. Dies war ein chaotischer und sehr ineffizienter Prozess. Es wurde von ein paar Leuten durchgeführt und es war unmöglich, die Späne sauber abzulassen. Es bestand auch die Gefahr, dass Kühlmittel auf dem Werkstattboden verschüttet wurde. Wir hatten auch eine Vollzeit-Wartungskraft, die das Kühlmittel in den Werkzeugmaschinensümpfen nachfüllte “, erklärt Ashley Mizen.
Das Wogaard-Kühlmittelrecyclingsystem wurde dem Unternehmen vom Vertriebsleiter Jason Hutt vorgestellt. Er erinnert sich: „Jeder bei Progressive Technology konnte die Vorteile der Installation des Kühlmittelsparers erkennen, aber die Arbeitsbelastung machte es schwierig, die Einheiten an den Maschinen anzubringen . Es dauert nur ungefähr 20 Minuten, bis sie passen, aber der Zeitplan war so eng, dass selbst eine so kleine Pause nicht gefunden werden konnte. “
Ashley Mizen fügt hinzu: „Wir haben eine ausgewählte Maschine angehalten, um den Kühlmittelsparer einzubauen, als wir bei einem bestimmten Auftrag ein Problem mit dem Kühlmittel im Spänebehälter festgestellt haben. Wir waren uns nicht sicher, wie lange es dauern würde, bis es passt, und zögerten, eine Maschine während unserer geschäftigen Zeit anzuhalten. Wir stellten fest, dass das Anbringen der ersten Testeinheit an der Maschine keine Zeit in Anspruch nahm, aber das Ändern unserer Spänefächer, um sie an den Kühlmittelsparmodus anzupassen, war der zeitaufwendige Prozess. Wir haben das erste Gerät einige Wochen lang getestet und konnten sofort feststellen, dass es einfach zu handhaben ist und mit unserem mit Wasser mischbaren Kühlmittelgemisch zwischen 6 und 9 Prozent ein Vermögen gespart hat von reduzierten Sumpfaufladungen und verbesserter Haushaltsführung. “
Neben einem Kühlmittelsparer, der speziell für CNC-Langdrehautomaten im Schweizer Stil entwickelt wurde, entwickelt Wogaard auch ein Spänebehältermodul, das die Installation des Systems wesentlich effizienter macht.
Jason Hutt fasst zusammen: „Wir wissen, dass vielbeschäftigte Unternehmen wie Progressive Technology immer Schwierigkeiten haben werden, die Zeit für die Installation unserer Kühlmittelspareinheiten zu nutzen. Deshalb entwickeln wir zusätzliche Geräte, um diese so schnell und einfach wie möglich zu gestalten. Neben dem Spänekorbmodul bieten wir auch maßgeschneiderte Fittingsätze an, sodass bei Bedarf alle für eine bestimmte Werkzeugmaschine erforderlichen Fittings mit dem Kühlmittelsparer geliefert werden . "