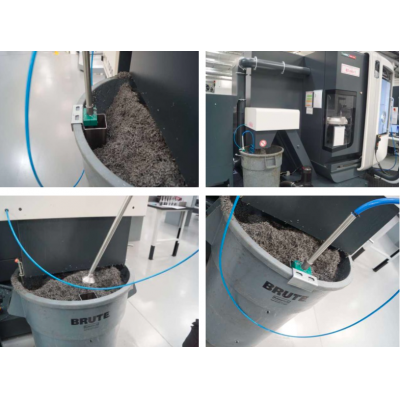
Wogaard-kylmedelsspararen används i Progressive Technology.
Genom att erbjuda avancerade CNC-bearbetningstjänster för de flesta av de ledande högteknologiska industrisektorerna har Newbury-baserad Progressive Technology, i metoder och förmåga, skiftat avsevärt från var företaget startade. Geografiskt har det dock knappast rört sig eftersom familjeföretaget ursprungligen etablerades i Overton, strax utanför Basingstoke, mindre än 30 minuter bort. När företagets ägare tog över den lilla jig- och verktygsverksamheten från fadern 1995 investerade han i EDM- och CNC-bearbetningsteknik för att stödja kundernas behov vid den tiden.
Sedan investerade företaget för cirka 7 år sedan i 5-axlig CNC-bearbetningsteknik när en Newbury-baserad Formula One-komponentleverantör bestämde sig för att lägga upp sina verktyg. "Vi förvärvade byggnaden och några av maskinverktygets tillgångar", påminner förbättringsingenjören Ashley Mizen. "Även om vi inte tog över verksamheten. Motorsportskunderna tittade på oss för att fylla det gap som hade lämnats. Vi hade utrustning och kapacitet, så vi tillämpade vår tekniska kunskap på de olika projekten och det växte därifrån.
"Därefter hade vi den 5-axliga platsen i Newbury, och de roterande och vertikala fräsmaskinerna i Overton. Vi fortsatte att gå från styrka till styrka och flyttade allt fräsning till den ursprungliga Newbury-webbplatsen. När fler maskiner köptes kom det till en punkt där vi kunde passa, så vi började titta runt Newbury för andra platser och köpte sedan vår nuvarande anläggning för ungefär tre år sedan. "
Efter ett omfattande renoveringsprogram var den 5 000 m2 stora enheten redo för ockupation, men fönstret med möjlighet att flytta mellan motorsports säsong var bara två veckor. "Vi flyttade de verktyg vi behöll och ersatte några andra. Vår gamla Mikron uppdaterades med en ny Mikron HPM600U. Två nya DMG 40 eVos tillsammans med två nya DMG 60 eVos fogades också till anläggningslistan, säger Ashley Mizen.
Denna investeringsfilosofi har fortgått när företaget har vuxit, med tre CMS 5-axliga mönsterskärningscentraler tillagd tillsammans med två nya 5-axliga Hedelius-bearbetningscentraler och en DMG DMU 50. Han fortsätter: "Vi är en snabbreaktionsverksamhet; Vi har en orderbok som tenderar att fluktuera mycket. Arbetar med alla stora F1-team, investerar vi ständigt i ny teknik. Vi anger våra maskiner väldigt mycket, med många extra funktioner som ingår för att göra dem så effektiva och mångsidiga som möjligt. "
Idag går den 60-starka kvalificerade arbetskraften 7 dagar i veckan, 24 timmar om dygnet. Materialskärning omfattar ett komplett sortiment av plastplast, rostfritt stål, värmebehandlade verktygsstål, 7-serie aluminium-, titan- och värmebeständiga legeringar, såsom Inconel, samt kiselintegrationsmetallmatriskompositer med PCD-verktyg. All personal är bemyndigad och betrodd att leverera, som Ashley Mizen säger "det handlar om att se till att rätt jobb går till rätt ingenjör".
Batchstorlekar varierar, motorsportkunder kan beställa 12 delar; sex av varje hand, medan precision medicinska komponenter normalt är 500 avstånd. "En av de största problemen för oss är att vi använder mycket högtryck genom spindelkylvätska, så maskinerna tenderar att översvämma om vi inte håller spåntransportörerna hela tiden. Men det fyller snart svärfackarna med kylvätska. "
"När reglerna för skrotmetall ändrats nyligen bestämde vi oss för att använda en leverantör av en enda källa, men de ville inte ta vårt skrot blött. Vi hade ett system där svetsfacken laddades på en enhet och tippades upp för att dränera. Detta var en rörig och mycket ineffektiv process. Det utfördes inuti av ett par personer och det var omöjligt att dränera svärven rent. Det hade också potential att orsaka fara på grund av kylvätska som spillde på verkstadsgolven. Och vi hade också en heltidsanställd person som fyllde kylvätskan i maskinverktygssummorna, förklarar Ashley Mizen.
Wogaard kylmedelsåtervinningssystem introducerades för företaget av försäljningsdirektör, Jason Hutt, som påminner om: "Alla på Progressive Technology kunde se fördelarna med att montera kylspararen, men arbetsbelastningen gjorde det svårt att få enheterna monterade i maskinerna . De tar bara ungefär 20 minuter för att passa, men schemat var så tätt, även en sådan liten paus kunde inte hittas. ”
Ashley Mizen lägger till: ”Vi stoppade en vald maskin för att passa på kylvätskespararen när vi identifierade ett problem med kylvätska i trasan på ett visst jobb. Vi var osäkra på hur lång tid det skulle ta för att passa så var ovilliga att stoppa en maskin under vår livliga period. Vi fann att det faktiskt inte tog någon tid att anpassa den första testenheten till maskinen, men det var den tidskrävande processen att ändra våra spånfack för att passa den kylmedelsspararen. Vi testade den första enheten i några veckor och kunde genast se nyttan, den är enkel att använda och med vår blandbara kylmedelsblandning på mellan 6 och 9 procent har det uppenbarligen sparat oss en förmögenhet, med fördelen av minskade sump top ups och förbättrad hushållning. "
Förutom en kylmedelssparare som är speciellt utformad för CNC-svarvar i schweizisk stil, utvecklar Wogaard också en modul för skaftfack som gör installationen av systemet mycket effektivare.
Jason Hutt avslutar: ”Vi vet att upptagna företag som Progressive Technology alltid kommer att kämpa för att få tid att passa våra kylvätskesparande enheter, så vi utformar tillbehör för att göra det så snabbt och enkelt som möjligt. Utöver modulen för spånfack kommer vi också att erbjuda skräddarsydda beslagsatser, så vid behov kommer alla rörbeslag som behövs för ett specifikt maskinverktyg att levereras med kylvätskespararen. ”