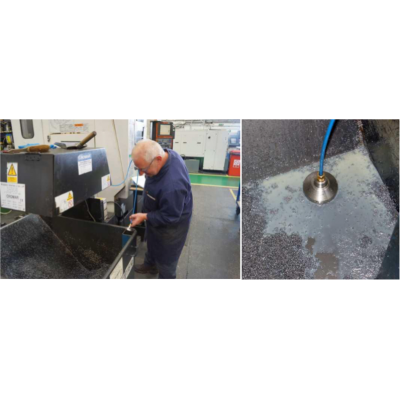
De Wogaard- koelvloeistofbespaarder heeft Cook Compression tijd en geld bespaard.
The Dover Corporation is een van de grootste wereldwijde engineeringbedrijven; het bestaat uit meer dan 500 bedrijven die in totaal ongeveer $ 8 miljard per jaar omdraaien. Als een strategisch onderdeel van de multinationale Dover Corporation biedt Cook Compression Group oplossingen voor de wereldwijde zuigercompressormarkt. Vanuit haar faciliteiten in Ellesmere Port ondersteunt Cook Compression klanten in de energiesector en is het Center of Excellence van de groep voor plaatkleppen.
Gebruikt in industriële dubbelwerkende zuigercompressoren, fungeren plaatkleppen als veerbelaste terugslagkleppen. De dubbelwerkende zuiger zorgt voor aanzuiging en afvoer en de drukverschil zal de zuigklep sluiten en de afvoer openen om het gas te laten bewegen. Deze geavanceerde compressoren worden gebruikt door bedrijven die een efficiënte gasoverdracht nodig hebben, zoals grote olie- en gasraffinaderijen.
Compressoren van dit type moeten in het veld lang meegaan, zodat het plaatventielmateriaal correct moet worden gespecificeerd en nauwkeurig moet worden vervaardigd. Dat gezegd hebbende, Cook Compression biedt ook renovatie- en upgrade-ondersteuning voor zijn klanten.
Plant Manager, David Wain, zegt: “Het belangrijkste materiaal voor kleppen is 416 roestvrij, maar we bewerken ook 420 roestvrij, 17 / 4PH, 300-serie roestvrij en gietijzers. Ventielinternals zijn gemaakt van 420 roestvrij en technische kunststoffen, zoals PTFE, PEEK en Nylon. Afhankelijk van wat de klant comprimeert, worden verschillende materialen gespecificeerd, zodat de gassen het klepplaatmateriaal niet aantasten en corroderen. We hebben veel aandacht besteed aan de R&D van nieuwe materialen om de prestaties van het comprimeren van verschillende soorten gas te verbeteren. Sommige compressoren lopen droog terwijl anderen worden gesmeerd, dit heeft invloed op de materiaalkeuze van de klep voor verschillende toepassingen. ”
Om zijn producten te produceren, beschikt het bedrijf over een aanzienlijk aantal CNC-bewerkingsmachines op locatie, waarbij de belangrijkste machines de klok rond draaien. "Cook is de afgelopen 10 jaar met ongeveer 15 procent op jaarbasis gegroeid, dus we hebben geïnvesteerd in nieuwe productietechnologie, waardoor de hele fabriek efficiënter is geworden", legt David Wain uit.
Hij vervolgt: “Met inbegrip van de twee nieuwe Doosan-werktuigmachines die recent zijn geïnstalleerd, hebben we 17 CNC-machines op locatie, die variëren van 2-assige CNC-draaibanken tot meerassige draaibanken en bewerkingscentra. We hebben ook een Kasto Twin A2 CNC-lintzaag die materiaal tot 300 mm diameter kan snijden.
“De zaag is een zeer betrouwbaar stuk kit. Het consumeerde echter een aanzienlijk deel koelmiddel vanwege de kleine chips die het op de spanenbaan slepen. We hadden de Wogaard- koelvloeistofzuiger gezien toen Business Manager, Jason Hutt, ons de voordelen kwam uitleggen. Hij stond ons toe om er een op proef te hebben, hoewel er geen eerder geval was dat de eenheid op een CNC-zaag werd gebruikt. Het enige vraagteken was de grootte van de pomp, maar we hebben het geprobeerd en het heeft echt dividend betaald. ”
Voorafgaand aan de installatie van de koelvloeistofbespaarder, moest de zaagoperator Matt Hollins een aftapkraan gebruiken om koelvloeistof uit de spanenbak te verwijderen, met behulp van een vat van 5 liter om het op te vangen en de koelvloeistof terug in de tank te porren, hopelijk zonder te morsen veel op de vloer. Omdat het afvoergat zich ongeveer 6 mm van de bodem van de bak bevond, bleef er altijd een residu achter in de bak, dus het was geen ideale methode.
De koelvloeistofbespaarder is via een flexibele leiding verbonden met de koelvloeistofpomp en wordt eenvoudig in de spanenbak van de zaag geplaatst. Wanneer de machine draait, wordt de koelvloeistofpomp gebruikt om een vacuüm op te wekken door de Wogaard-eenheid, die de koelvloeistof eenvoudig terug uit de bak en terug in de tank van de machine trekt. "Met de koelvloeistofbespaarder zijn de bakken nu bijna leeg wanneer we ze controleren", zegt Matt Hollins. "We vulden de tank een keer per dag met 25 liter, dit is teruggebracht tot een keer per week, of maximaal twee keer per week als het meer dan twee ploegen draait."
Dat was het succes van de koelvloeistofrecyclingkit op de band zag dat het bedrijf besloot om een Wogaard-eenheid op elk van zijn werktuigmachines te monteren. Een van de eerste die werd gemonteerd was een verticaal CNC-bewerkingscentrum van Mazak Nexus, zoals machinebediener Joe Diggery herinnert: “We vulden de tank van die machine één keer per dag met ongeveer 50 liter, en nu is het slechts twee of maximaal drie keer per week. "
Droge spanen hebben nog een voordeel voor het bedrijf, zoals HSHEQ (Health and Safety, Hygiene, Environment and Quality) Manager, Phil Avis, verklaart: “De spanenbakken worden twee keer per dag geleegd als de machines bijna leeg zijn. De spanen worden verzameld door een recyclingbedrijf en het koelmiddel dat in de bakken achterbleef, moest in IBC's worden gegoten voor correcte verwijdering. Dit bracht natuurlijk extra kosten met zich mee. ”
Hoewel het bedrijf nog steeds de besparingen bewaakt die zijn bereikt met de koelvloeistofbesparing , toont een ruwe berekening een besparing van ongeveer één vat koelvloeistof per maand, wat een terugverdientijd van minder dan 6 maanden oplevert.
Phil Avis concludeert: "Installatie is eenvoudig, vooral nadat je er een hebt gedaan. Omdat we ze hebben laten monteren, zijn de operators niet alleen blij met de resultaten, maar het zal ook een grote impact hebben op ons milieu, vooral als we ISO nastreven 14001 accreditatie. We willen alles op zijn plaats krijgen voordat we de auditors inschakelen, en met dit project dat gesleepte koelvloeistof effectief terug in de machines kan worden gepompt, is het een win: win-situatie. ”